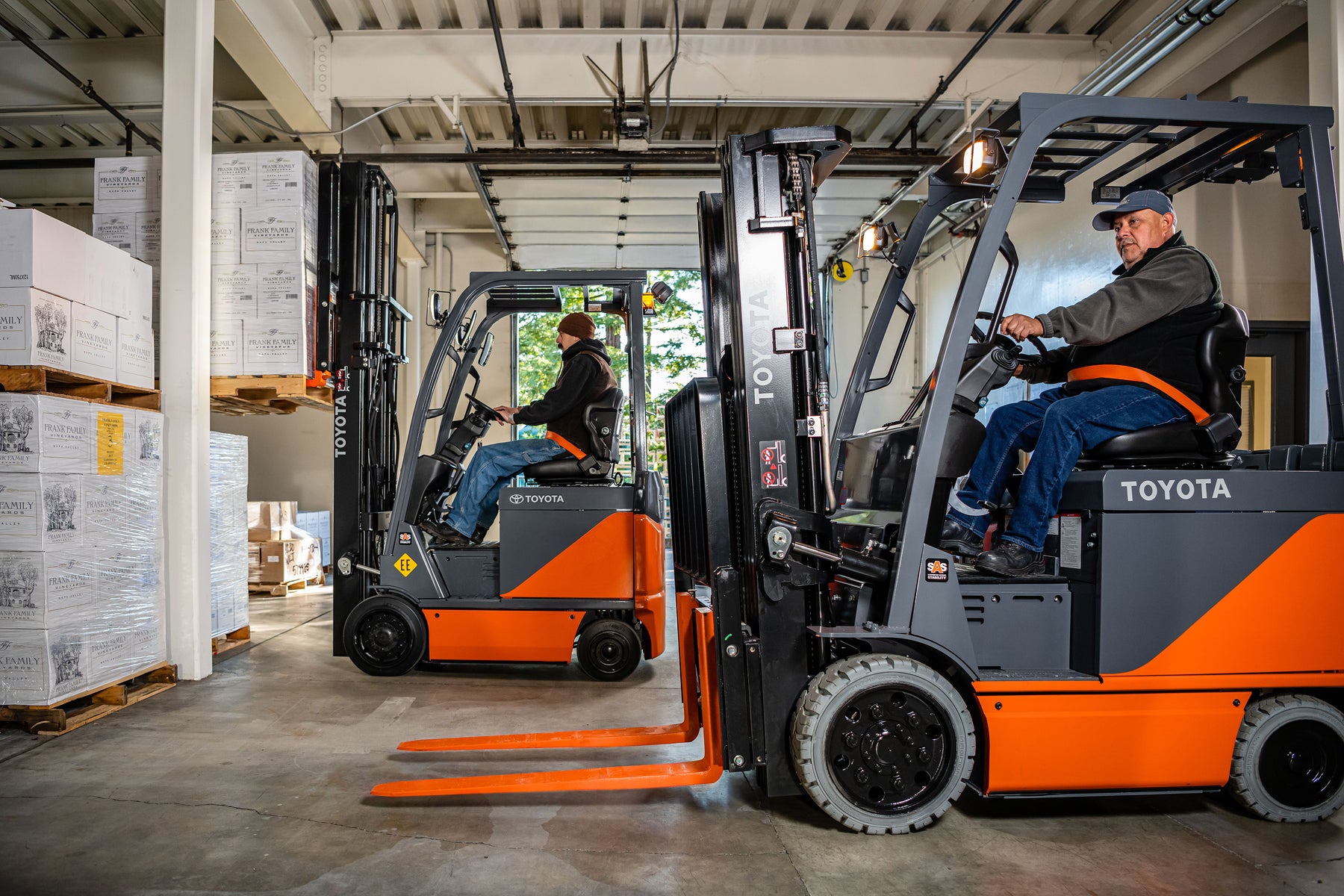
How Ergonomics and the Right Equipment Can Benefit Your Business
The word "ergonomics" has worked its way into the popular lexicon during the past decade or so, but this concept — the art and science of shaping manufactured objects around the needs of human users — has been in circulation since the Stone Age. Human hands, feet, backs, shoulders and heads should not be forced to change their design to adapt to factory equipment or manufacturing tools. The adaptation process needs to move in the other direction if workers are expected to produce, carry, lift, and work at their optimum capacity.
Here at Liftow, we understand the importance of ergonomic data and the application of that data in the design of functional lifting equipment. The best lifting machinery, including lift trucks, will always be the equipment that users can operate comfortably and safely. And since the materials handling industry often involves repetitive motions and sustained positions that can last for hours at a time, we view intelligent ergonomics as the first line of defence against workplace injury and illness. We also recognize that smart ergonomics lead to productive workers who stay in motion and keep the company bottom line elevated.
Are you factoring ergonomics into your lift truck purchase and rental decisions? Things like fuel mileage, depreciation, and maintenance costs are often taken into account by managers making an equipment decision. But are you also factoring in the lifetime value this equipment will produce if workers are comfortable in the operator’s seat and can easily reach controls and signalling indicators?
Preventing Musculoskeletal Disorders
MSDs, or disorders of the muscular and skeletal system, are the most common form of workplace injury brought on by poor ergonomics. And the best form of protection against these issues will come from a strong ergonomics program that includes the following considerations.
- Provide proper training. If workers are using equipment correctly from the start, then slight maladaptations and misalignments between the equipment and the body can be corrected before they become serious problems.
- Encourage early reporting. If workers begin to feel tension, tightness, tingling, stiffness, numbness, or pain in any area of the body that’s subjected to repetitive motion in the workplace, make sure they know where and how to report this problem and get help before the injury gets worse.
- Don’t just listen—act. If workers experience the beginning stages of a workplace-related MSD, reevaluate the equipment that created or exacerbated the problem. Complete the repairs and adjustments necessary, or replace the equipment.
Leave a comment